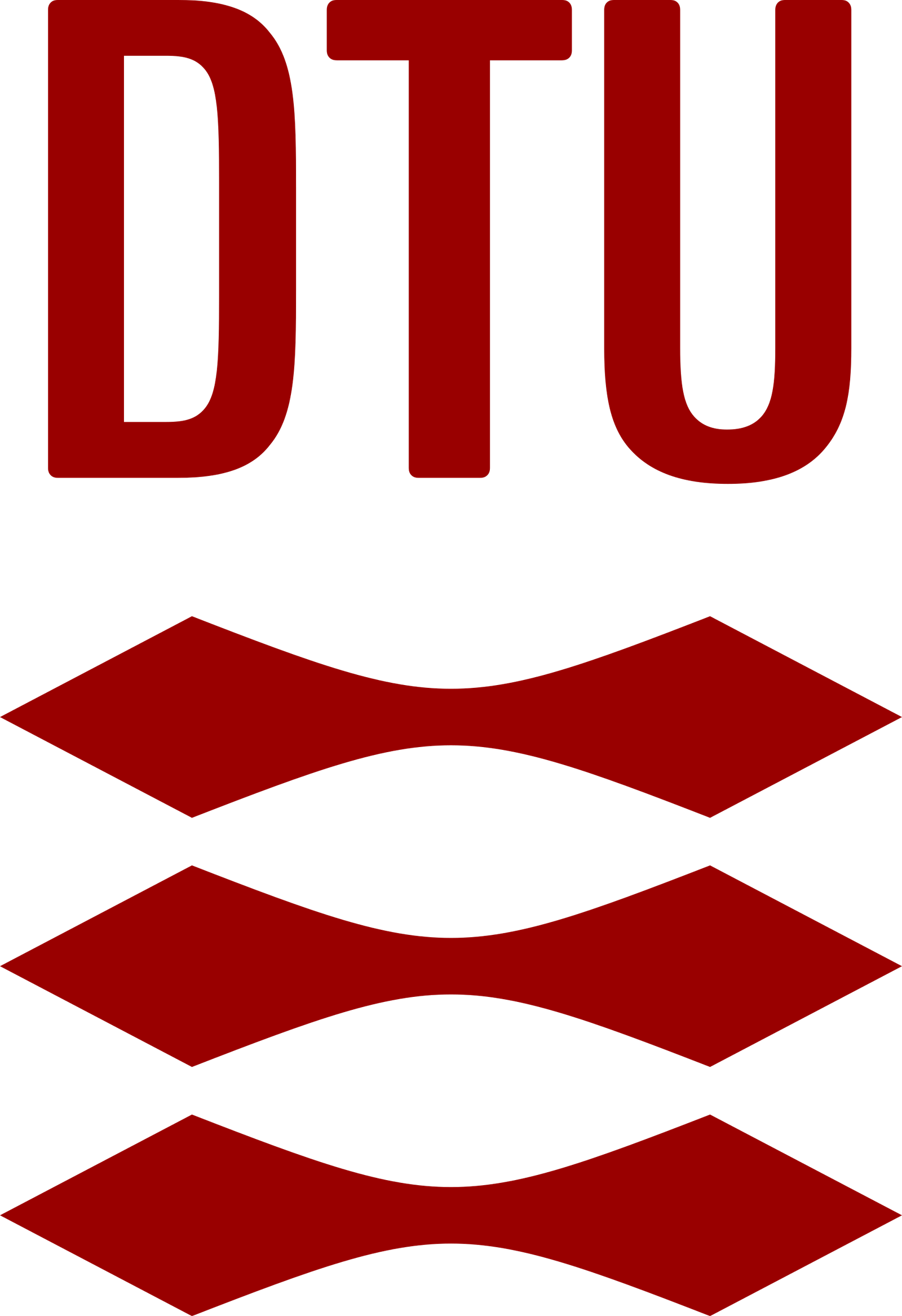
Peter Behrensdorff Poulsen is chief scientific officer and group leader of the solar photovoltaics systems group at DTU Electro. He is also founder and CEO of Danish PV Service

Alexander Fraess-Ehrfeld is the CEO and Founder of AIR6 SYSTEMS, a leading company that develops and produces industrial drones for various industries and applications.
Background
Climate change is showing its impact through increasingly frequent and intense weather events, such as heatwaves, droughts, and severe storms, disrupting ecosystems and human activities. Rising sea levels are threatening coastal communities while shifting temperature and precipitation patterns are impacting agriculture, biodiversity, and public health. These changes underscore the urgency of adaptive and mitigative strategies to combat climate-related risks across the continent. Photovoltaics (PV) is a key technology to battle climate change by replacing fossil fuel with clean energy, and its capacity is expected to grow 10-fold globally from today to 2050 and comprise 56% of grid-connected generation capacity. Such fast and massive deployment of solar PV comes with its own reliability risk and must be accomplished wisely to ensure minimum loss of valuable green energy.
Imaging and inspection technologies for PV systems
Due to their long operation in changing outdoor conditions, PV modules are prone to a variety of degradation mechanisms over their operational lifetime. Precisely measuring, detecting, and understanding these mechanisms is crucial for operational optimization and maintenance planning. The current PV plant O&M best practices suggest an annual infrared (IR) thermography inspection and usage of electroluminescence (EL) imagery for a root cause analysis of detected anomalies. Luminescence-based imaging techniques like EL, photoluminescence (PL) and EL spectroscopy have become a standard inspection of silicon-based solar cells, especially in production lines of PV modules, to verify the quality of produced cells. But also, on PV modules in operation, luminescence techniques experience an increased usage, due to their high detail. The challenge is to utilize the wide range of imaging techniques most efficiently to identify common defects such as cell cracks, delamination, electrical circuit corrosion, and others and predict their impact on performance.
Solaris Project
At DTU, we contribute to SOLARIS with advanced methods for condition monitoring and inspection of PV modules, particularly focusing on luminescence-based imaging techniques. Our team leads the development and field demonstration of automated drone-based inspection systems that integrate high-resolution visual, thermal, and luminescence sensors. These systems enable rapid fault localization with enhanced spatial accuracy and support predictive maintenance strategies. In collaboration with AIR6 Systems, we are integrating custom EL and PL hardware directly onto rugged inspection drones, enabling fully automated and high-resolution inspection of PV systems in the field. This setup allows for rapid fault detection — even in daylight conditions — without the need for manual disassembly or power shutdowns.
Trial inspection at DTU
In the last days of April trial inspections were done at the 0.5MWp PV power plant at DTU Risø campus which acts as test and demonstration site in the SOLARIS project. The AIR4 Rugged drone was used for the luminescence inspections and the novel AIR4 Nano drone, weighing only 380 grams with 13.5 cm dimensions (length/width), was used for the thermal inspections. Both systems were supplied from AIR6 Systems.
Luminescence inspections were done both daytime and nighttime to back-powering the solar panels with a power supply for bringing them into a luminescence state that can be seen by a short wave infrared camera mounted onto the drone. By modulating the power from the power supply, and running the camera in video mode, several images are taken of each PV module which in postprocessing can be treated so noise from the sun can be subtracted leaving daylight luminescence inspection possible which was successfully done during the trial inspection.
Image processing
The acquired images were afterwards corrected and processed by DTU’s luminescence imaging processing tool and below is shown a comparison of images of the same cracked PV module taken indoor and outdoor using both a tripod and drone for carrying the camera. The outdoor inspections were done both during nighttime and daytime.
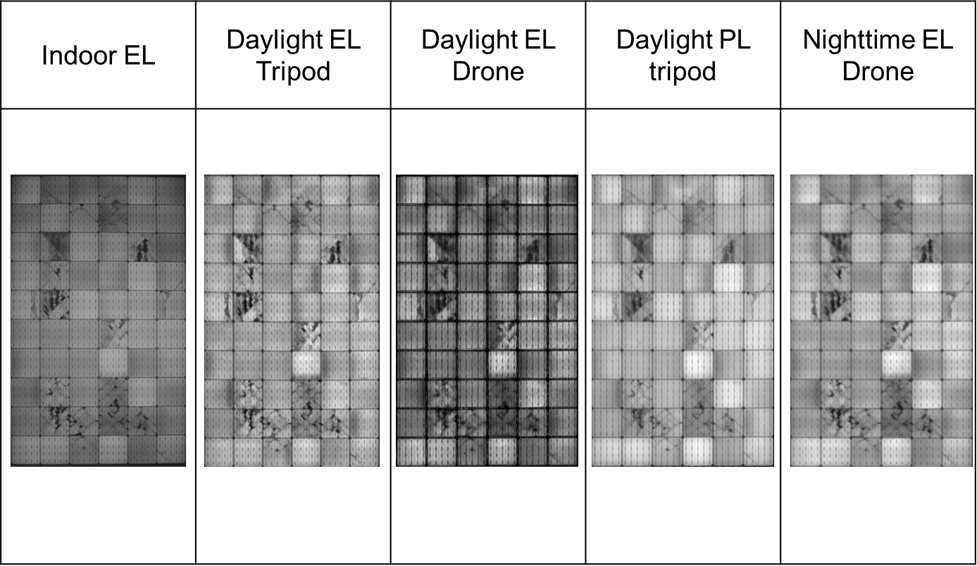
IR images were also acquired by Air4 Nano drone and where an example is shown below:
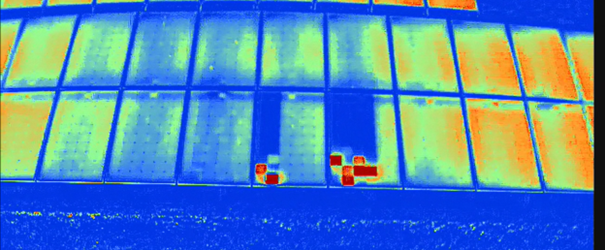
The partners are working on enhancing the quality of the images acquired from the drone and the algorithms used for improving the quality of the images before the drone later on will be used for inspection of the 3 commercial test facilities in the project.
Digital infrastructure
We also develop the foundational digital infrastructure for data handling in SOLARIS, including real-time integration of inspection data into an IoT-based asset management platform. The platform supports AI-based diagnostics and feeds into a decision-support system for PV operators. Our aim is to transition from reactive maintenance to data-driven and preventive asset management, ultimately improving the reliability and profitability of solar energy systems across Europe.